IDEATION
Where the Story Begins
At the very beginning , our talented artist Sunyu had already got an idea for the automaton in his mind which was making a elegant ballerina doing fouette turns. We all liked this idea, so we directly started the Post-It-Notes ideation process. After brainstorming, we finally had the theme, which was a ballerina doing fouette on a walking swan.
![]() Post-It-Note | ![]() Post-It-Note | ![]() Post-It-Note |
---|---|---|
![]() Post-It-Note | ![]() Post-It-Note | ![]() Post-It-Note |
FIRST INSPIRATION
After we had the theme for our automaton, I spent a lot of time thinking about the mechanism we should use for the fouette motion. However, nothing came to mind until an easy ECE 310's lecture. Since that lecture was quite easy, I got bored and started thinking something else. All of a sudden, a brilliant idea just popped into my head. Then, I drew it down and that's how our first inspiration came from.

FROM IDEA TO DIGITALÂ WORLD
From 1 to 2
After all my teammates agreed with my idea, I started converting the from paper to Creo. Actually, it was much harder than I thought it would be. Even though we had a pretty complete idea, some details, such as gear ratio and connection method, were still a pain in the butt. After more than ten hours' struggling, I finally finished our first Creo design.

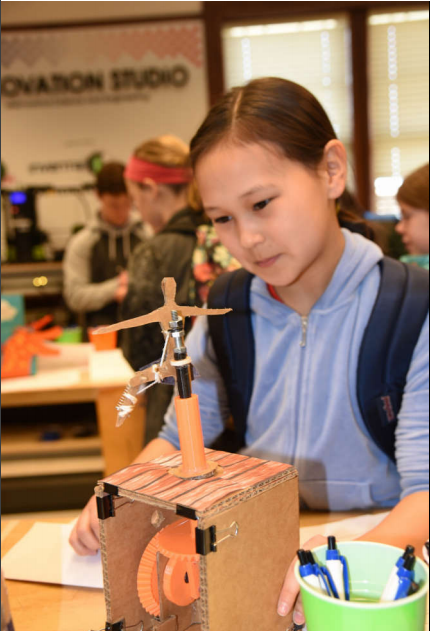
Credit to Professor Liebenberg
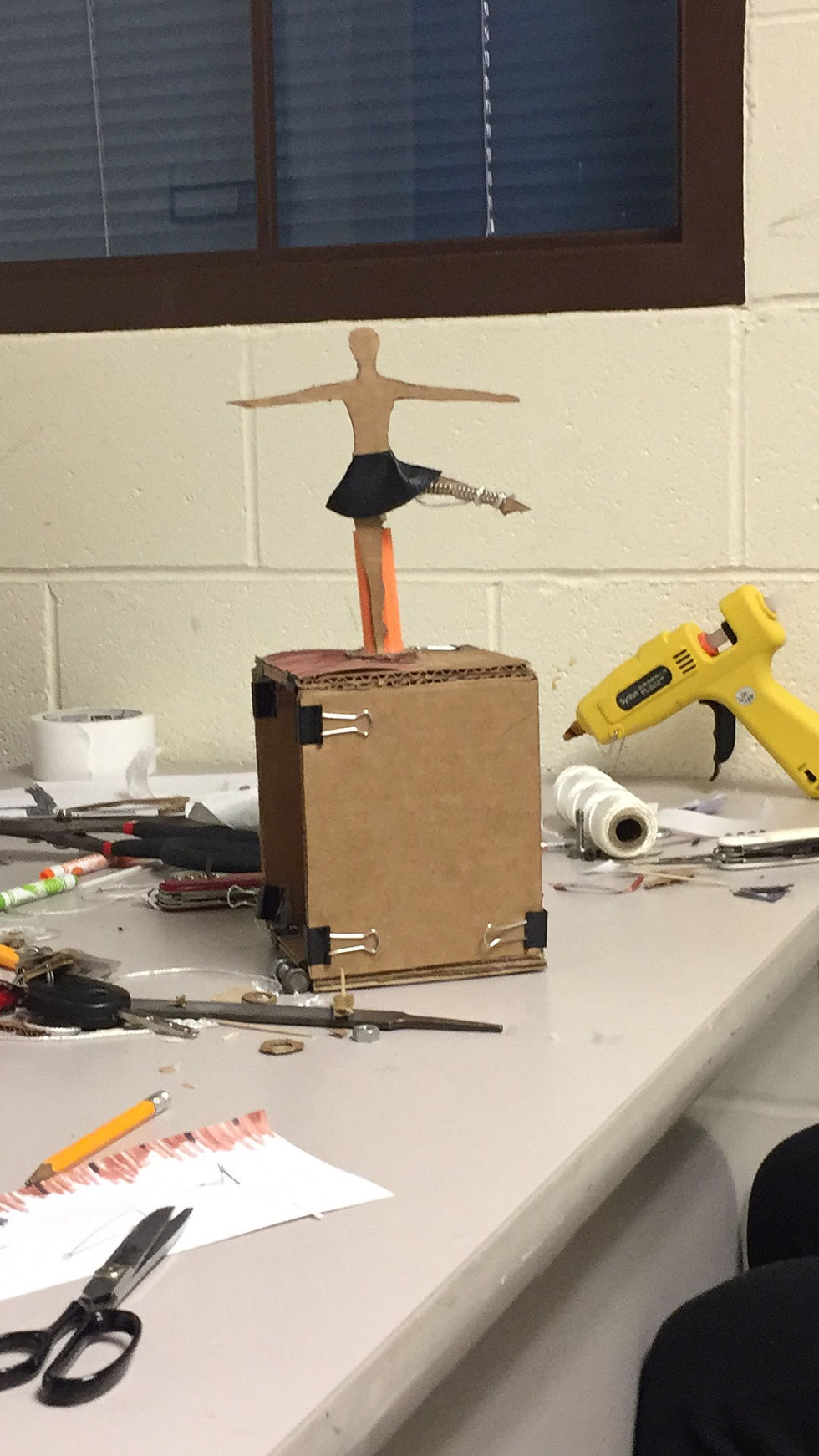
Credit to Jiheng Jing
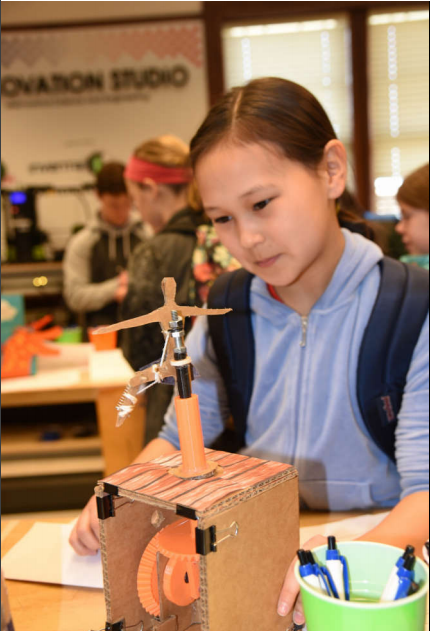
Credit to Professor Liebenberg
FROM DIGITAL WORLD TO REAL WORLD
From 2 to 100
After we had our Creo design, we started making it in the digital world. Once again, it was much harder than I thought. This time, we have met a lot of real world issues, such as the rod was not smooth enough and the top plate was not flat enough. Finally, after we solved all the real world issues, we proudly presented an elegant ballerina in Engineering Open House and received a lot of praise.
In this automaton project, we used a four bar linkage mechanism to control the main shaft which can move up and down so that it can control the leg motion. As for the body rotation, we used a set of bevel gears to change rotation's direction. By doing this, we successfully imitate the ballerina's motion.

WALKER DESIGN
From 100 to 0
After Engineering Open House, we started designing the walker as well as the new version of our automaton that can be place on the walker. This time, my teammates Alan and Ian took over the design and I started working on PVA and DFA analysis of our leg mechanism. After a month's design, we finally had our Creo model for the walker.

Credit to Sunyu Wang

Credit to Sunyu Wang

Credit to Sunyu Wang
WALKER MANUFACTURING
From Simulation to Real World
After we finished designing the walker and automaton, we started making them in real world. This time, as we have expected, we met a lot of challenges in real world. For example, with this chassis design, our walker was really hard to walk on the grass robustly. What's more, our ground link's orientation was wrong, which means our walker can't walk as well as we expected. This time, I think we made a mistake. Instead of immediately redesigning the chassis, we chose to keep using it because we thought it would be good enough. I believe this strategy mistake was one of the key points which led us to the failure in the final competition.

Credit to ME 370 Instructors
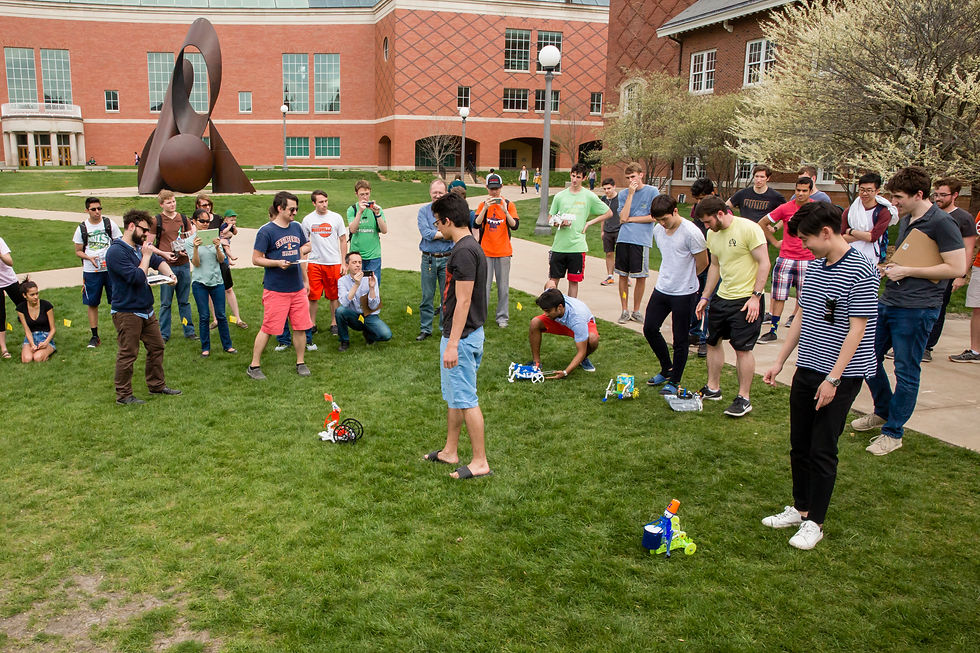
Credit to ME 370 Instructors

Credit to ME 370 Instructors
FINAL COMPETITION
Real World Real Challenge
Before final competition, our walker had already been able to walk on the grass. However, in order to make our walker better, we tested it with several different leg mechanisms. Some of the leg mechanisms were very long, which exerted a huge amount of torque on the motor as well as the gears. Since our gears were made out of Delrin, which is very soft, after those several tests, fatigue failures occurred at gears. Unfortunately, none of us noticed that issue. Thus, during the final competition, the gear that directly connected to the crank failed and our walker did not finished the competition.

CONCLUSIONS
Learning From Failure
After finished this project, I made a list of what we did wrong in this project in order to prevent them from happening again:
1. We should not let one person do one job. When we started designing the walker, we were separated to do different tasks. I did all PVA and DFA analyses by myself, Alan designed the whole chassis by himself, Ian redesigned the automaton by himself, and Sunyu did all artistic things by himself. This is definitely very efficient, but at the same time, it is hard for other teammates to find the implicit problems in one task. For example, if I made a minor mistake in PVA analysis, I believe no one would be able to find that because they did not get involve with that task. So I might be the only one who can find the problem. But since it is my work, it will be hard for me to find the minor mistake in my work. So I would recommend that next time we should have two person working on same task, which will significantly decrease the probability of making mistakes.
2. If we find a problem in our design, we should be able to admit it and change the design as soon as possible. For our project, we found some shortcomings in our chassis design a couple weeks before final competition. However, instead of changing the design and making a new one, we chose to keep working on this non-perfect prototype, which was one of the key point that led us to the failure in final competition. So in the future, once we have identified a problem in our prototype, we should design a new one instead of insisting on the non-perfect one.